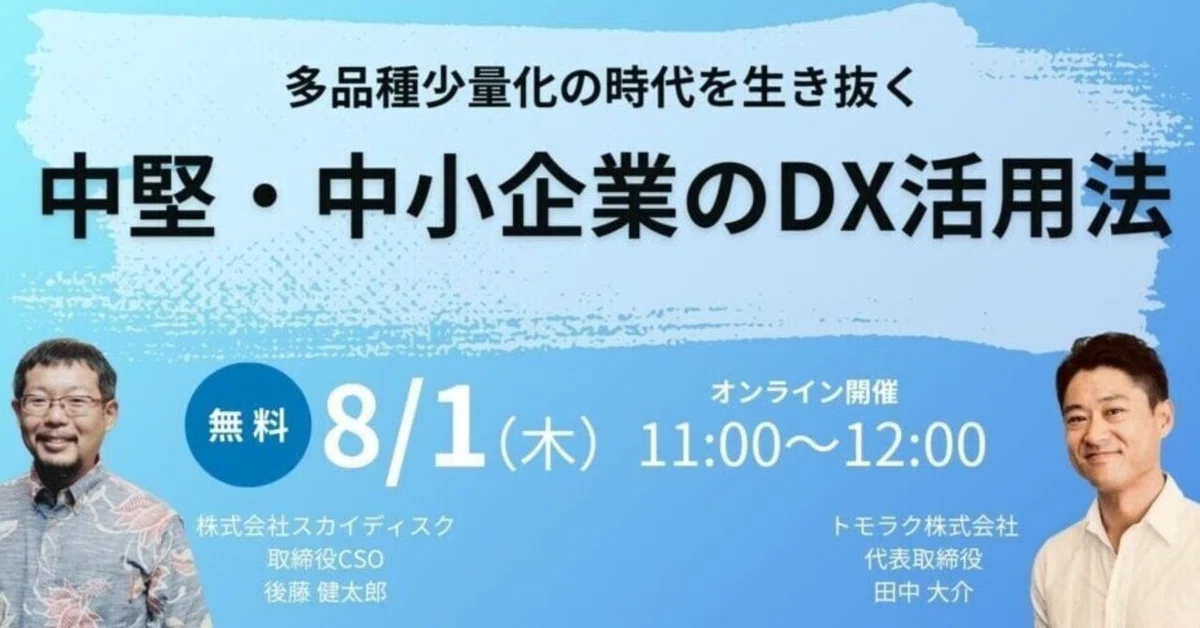
多品種少量化の時代を生き抜く中堅・中小企業のDX活用法(中編)
2025年03月28日 11:20
この記事は、2024年8月1日(木)に株式会社スカイディスク(登壇者 CSO 後藤健太郎)とトモラク株式会社(登壇者 代表取締役 田中大介)が共催したウェブセミナー「多品種少量化の時代を生き抜く中堅・中小企業のDX活用法」をトモラク株式会社が書き起こしたものです。
セミナーの一部の内容を要約・編集しております。予めご了承ください。
中編 目次
DXの取り組み方
うまくいくDX/いかないDX
設計領域のDXの進め方
DXの取り組み方
後藤さんはDXがうまくいくためには何が必要だと考えていますか。
(スカイディスク CSO 後藤)
そうですね。私はDXを始めるときの最初の一手は『可視化』が重要だと考えています。
可視化ができて初めて改善対象がわかり、効率化を図ることができるということですね。
これまでの現場の改善というのは、稼働状況や工程の分数を確認して、時間がかかっている工程にカメラを設置して改善ポイントを見つけて、誰でも効率的にできる手順に変えて、というようなことをやってきたと思うのですけれど、考え方は近いと思っています。
DXを通じて、可視化⇨分析⇨手順の改善、という支援をするということだと思います。図面管理や部品表の管理においても共通するものがあるのではないでしょうか。
一人一人の改善から組織としての改善へ
おっしゃる通りですね。これはお客様自身も認識されていて、よく「ノウハウはベテラン設計者の脳みそにあって、あの人がいなくなったら回らない」とおっしゃいます。つまりこれまでの改善活動は、一人一人の業務の改善に依存しすぎてきたのではと考えています。
ここからは、組織としての可視化・改善をする局面に入ってきたのではと。
後藤さんがおっしゃる通り、設計の領域では図面や部品表などがまだ紙に印刷されて保管されていたり、スキャンしてPDFにはしたがファイルサーバーの中に入っていてベテラン設計者や設計した本人以外には利活用可能になっていないという状況が多いかと考えています。
設計のノウハウが組織として使えるようになれば、設計効率が上がり、設計コストが下がり、もっと言えば設計リードタイムが短くなります。最近では、お客様からの納期要求が厳しかったり、製品の開発スピードを早くしたいという声が強まっていると思いますので。
また、過去の設計資産を踏み台にできるということは、設計品質も上げやすいですよね。設計品質が上がれば、後々の設計変更を減らせたり、手戻りや仕損も減らせる可能性が出てくると思います。
特に多品種少量や一品一様のお客様の場合は品種が多いので1プロジェクトに使える時間がどうしても限られてきます。設計品質を上げる時間が限られていますし、そうなると購買や製造で手戻りが起きがちです。
設計部門のDX投資よりも、購買・在庫管理のDX投資を重視するお客様もいて、そこはお金に直結するので重要性はよくわかるのですが、やはり設計段階の改善インパクトが大きいのではと考えています。
結果をもたらす原因を考える
(スカイディスク CSO 後藤)
そうですね。結局は、その結果をもたらす「原因」が何かという話だと思います。在庫が余ってますっていう話があった時に、在庫を管理したいというのはわからないことでもないのですが、その「原因」ってなんでしたっけ?と考えると、設計変更などで使わない部品が出たとか、不測の事態に備えて安全在庫を持っておきたかったということもありえると思います。
つまり、結果をもたらした原因は「想定通り作れていない(だから安全在庫をたくさん抱えておきたいなど)」ということですよね。このように課題があるときに、どこからアプローチすると一番効率的に課題を解消できるのかは大事だと思います。
うまくいくDX/いかないDX
よくお客様から「うちではシステムを使いこなせない、定着しない」というお話を頂くのですが、後藤さんはこの点をどうお考えですか?
(スカイディスク CSO 後藤)
そもそもDXって前例として社内の誰かがやったことがあるわけではないので、うまくいくかどうかがわからない状態で始めていくものだと思っています。
ですから、正解が見通しにくい中で色々なことをカチッと決めようとしすぎると、手段であるはずのDXを進めることがいつの間にか目的になってしまうことがあると思います。こうなるとうまくいかないことが多いと思います。
例えば、弊社の手掛ける「最適ワークス」は生産計画を作るツールなので、カチっと計画を立てることに目がいくかもしれませんが、むしろ今まで生産計画を作っていたベテランの頭の中にしかないものを可視化していくことで、誰でも計画を立てて改善をしていける術を身につけられるツールだと考える方がDXの本質ではないかなと考えています。
あと、DXによってベテランやエース社員がよりクリエイティブな仕事をできるようになるという点も見逃せないポイントだと思います。人が想像力を使って努力するところと、そうじゃないところをDXで整理していくという観点も大切なことかなと思ってます。
こう考えていくと、費用対効果は必ず見合ってくるはずなので中長期的な目線でDXに向き合うことが重要だと思います。中長期の目線で取り組むわけですから、私たちはDXのプロジェクトを定期的に振り返り、改善をしていく場をシステムを導入いただいたお客様と設けさせていただいています。
ありがとうございます。非常に重要なポイントですよね。
設計領域のDXの進め方
先ほどの後藤さんの話とも繋がりますが、私たちは「小さく産んで大きく育てよう」とお話ししています。
将来の大きい効果が見込めるというのは当然、会社としても経営としても大事なのですが、いきなりステップなしにそこへ行こうとするとあれもこれもやらなきゃいけなくて、手が動かなくなる。じゃあどこからやるのかっていうことで、まずは今ある設計資産を見える化する、使える状態にするっていうところが一段階目です。
二段階目はそれを使って設計・開発スピード、品質、業務効率を上げていきましょうという提案をしてます。
さらにその先は、例えば保守サービスを新たな収益源にしたいなどを考えていけるようになると思います。
例えば、この部品はいつ保守しなきゃいけないですとか、そういったこともデータで能動的に保守計画を組んでお客さんにアナウンスをして、といったイメージです。
ただ、最初はカチッとしなくて良いのでデータを利活用可能な状態にしましょうと言っています。
例えば、Tomoraku DMSでしたら、今のフォルダ構成のままでも良いのでクラウドシステムに入れてください。そうしたら、図面文書内も含めてAIを用いて検索できるようにしますよ、それを営業や購買、製造とも共有して設計資産を活用できるようにしましょう。協力会社様にもセキュリティが担保された状態で共有できれば、業務が効率的になりますし、情報の伝達漏れなども減りますよね。
過去の設計資産を使えるし、自分も探す時間を減らせるし、他部門や協力会社様からの資料提供依頼などへの対応も減るし、こういうところが一丁目一番地ではどうでしょうか?と提案します。
その先って何があるの?といえば、設計承認や出図などの業務フローをデジタル化したり、コストや含有物質、規制情報を品番ごとに管理できるようにしたり、図面や資料をただフォルダに置くところから一歩踏み込んでみましょうという提案をしています。
さらには、エクセルのBOMをみて1部品ずつ図面や関連資料を探して、、、というのは非効率ですからシステム上でBOM管理をしていつでも構成部品の図面や関連資料を見れたり、構成部品のコストや含有物質量の集計をできるようにしたり、ある部品が生産終了になった時に、他でどこに使われているかっていうのを逆展開できるようにしたり、という提案をして、設計スピード、効率の改善をお手伝いしています。